Decoiler
At Fanty Machinery, we pride ourselves on delivering cutting-edge decoiler, servo feeder, press punch machine and automatic stamping solutions to elevate your manufacturing processes. Our Decoiler Product Group exemplifies our commitment to precision, efficiency, and innovation. Explore the subcategories, read the case studies, and find answers to your questions to gain a deeper understanding of how our decoilers or uncoiler can transform your operations.
Product Group Overview: Decoiler
Decoiler
To achieve the automated manufacture of coil material, the decoiler is primarily utilized in conjunction with punching, shearing, laser cutting, and cold bending forming machines. It can be configured as a production line for uncoiling, leveling, feeding (cutting) to satisfy the requirements of the stamping workshop, and it is appropriate for usage in the construction hardware, automotive components, home appliances, and metal products industries, among others.
One of the most crucial pieces of machinery in the stamping manufacturing line is the decoiler for metal sheet coils. It has two purposes: one is to rotate the straight head of the steel belt to send it to the leveler, and the other is to support the steel coil by tightening its inner hole. As a result, the decoiler's performance affects the entire production process. After many years of design work, the decoiler's structure has been refined and optimized, improving the device's performance.
What's A Decoiler?
A decoiler, also called uncoiler or unwinding machine, is a mechanical device designed for efficiently unwinding coils of various materials, such as metal, paper, or plastic. It plays a crucial role in production processes by providing a controlled and steady supply of material for further processing. Decoilers are equipped with features like adjustable tension control, guiding systems, and often work in conjunction with straighteners and feeders to ensure smooth and accurate material feeding. They are essential components in industries like metal stamping, roll forming, and coil processing, contributing to improved productivity and reduced material wastage.
Grouping of Fanty Decoiler
Designed for standard coil unwinding, capable of handling a range of materials and coil sizes.
Equipped with a hydraulic system to efficiently handle heavy coils, offering precise control during unwinding.
Engineered for substantial loads and larger coils, providing stability and reliable performance.
Simultaneously unwinds two coils, reducing setup time and boosting productivity.
Operated manually, suitable for smaller-scale applications or workshops with intermittent coil handling.
Flat Decoiler, Hydraulic Decoiler, Heavy Duty Decoiler, Double Head Decoiler, and Manual Decoiler are the five main types of uncoilers. In accordance with the breadth, thickness, load, inner diameter, and outer diameter of the relevant material, each model can be further segmented into numerous specialized models. As a result, after choosing the model based on the coil material's qualities and the process's features, the cost must be ascertained.
How can I select a decoiler for my stamping needs?
Finding an uncoiler that works for you usually involves three steps.
1. Determine the material's basic dimensions, including its inner and outer diameters, weight, width, and thickness.
By initially defining the material's fundamental characteristics, you may determine the kind of uncoiler or decoiler you require in general.
2. Recognize your own processing and manufacturing environment in order to select the decoiler setup.
a. Selection between motorized and non-motorized models
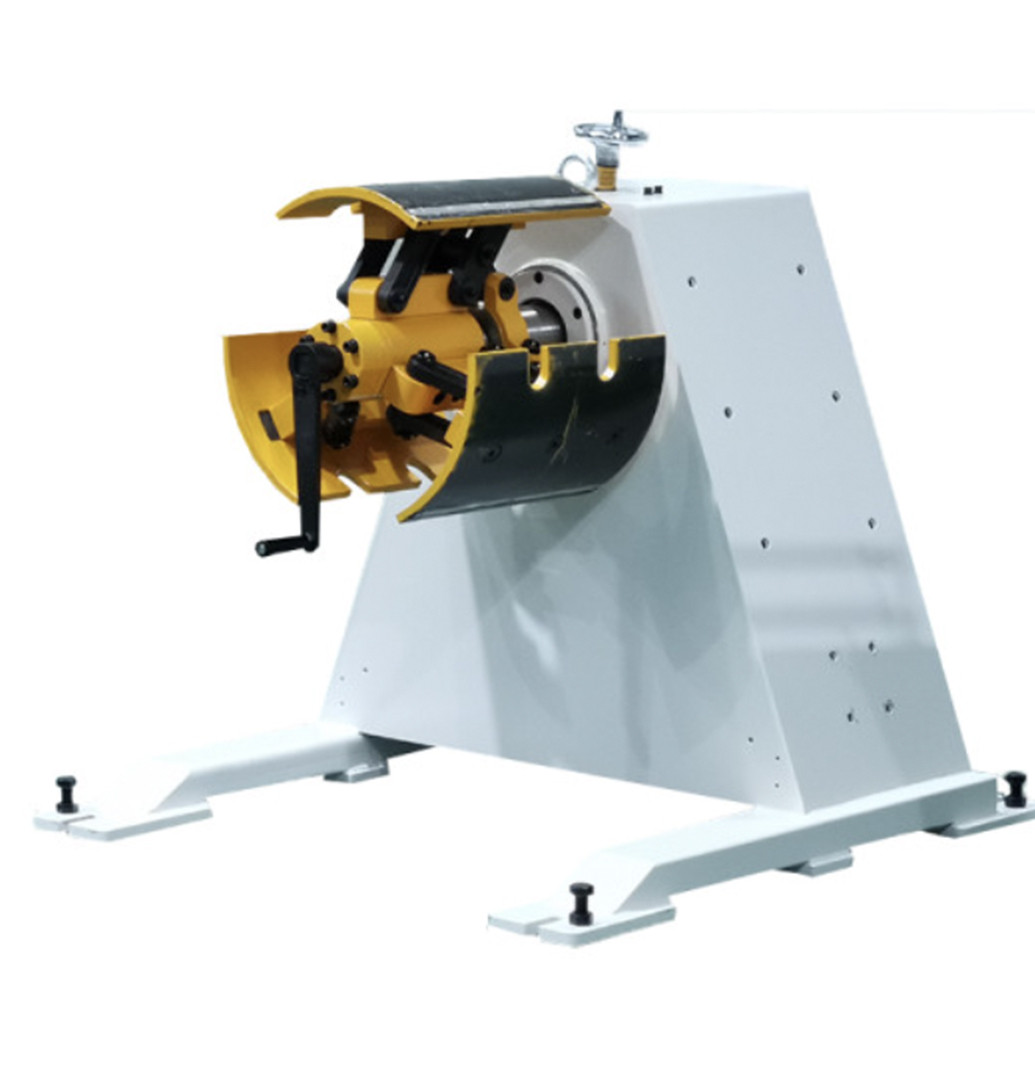
Unmotorized Decoiler Model: ① Manual Model (Comprising Brake Device)
Usually used just for unwinding; rewinding is not frequently used. Fundamentally, it is employed in a few specialized industries, like cold bending forming machines or punching shelves, silicon steel sheets, and EI sheets.
Unmotorized Decoiler Features: It can save floor space because a large waiting area doesn't need to be reserved, but it requires a lot of traction for the machines to work together, and the uncoiled material shouldn't be too thin because that will strain the material.
Motorized Decoiler Model: ② Control Panel-equipped Motorized Model.
It can be employed as a rewinder or decoiler, and most of them are utilized in conjunction with other machines such as laser cutting machines, punching machines, shearing machines, hydraulic presses, cold bending forming machines, etc. With a high degree of customisation, it can unwind coils of different widths and thicknesses on its own.
Motorized Decoiler Features: It's a widely used model with plenty of adaptability, high customization, and ease of matching with other machines.
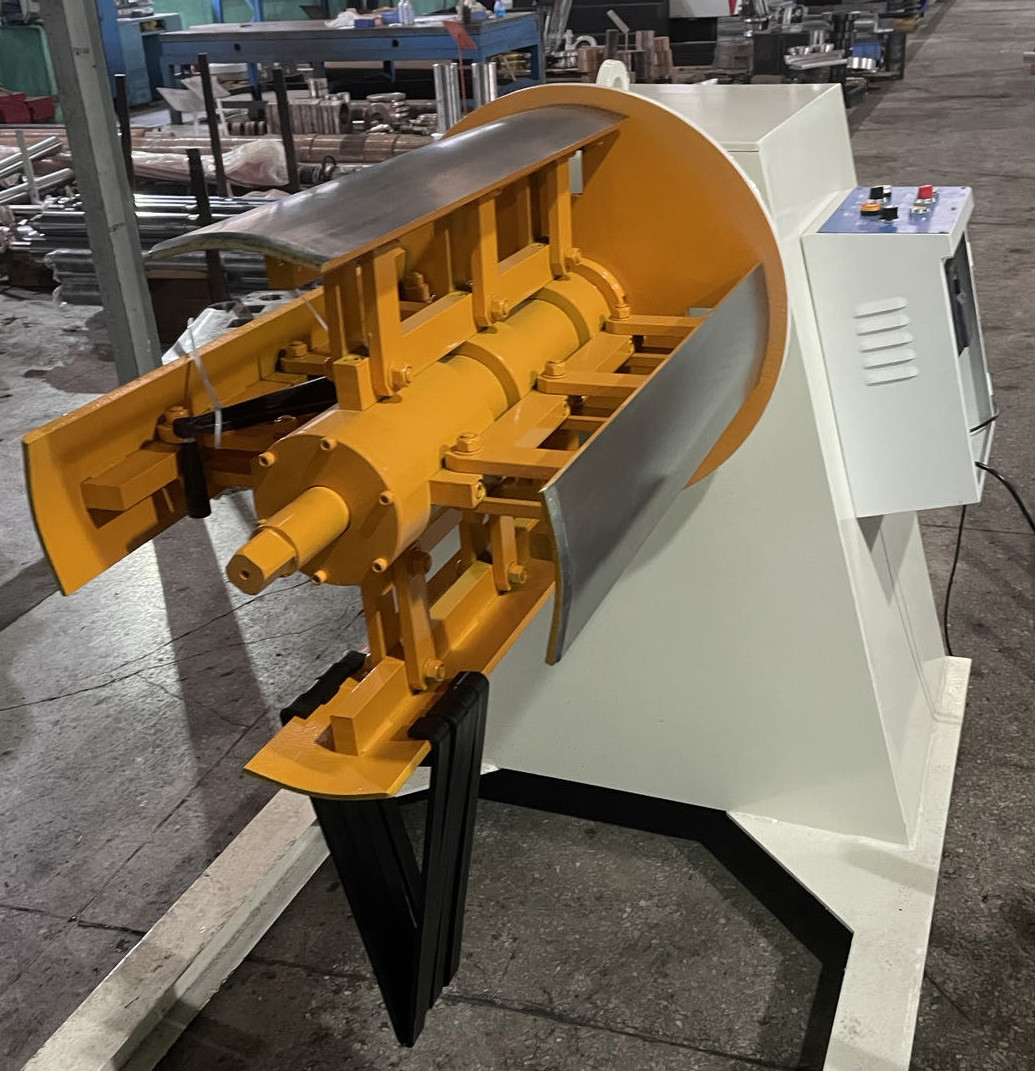
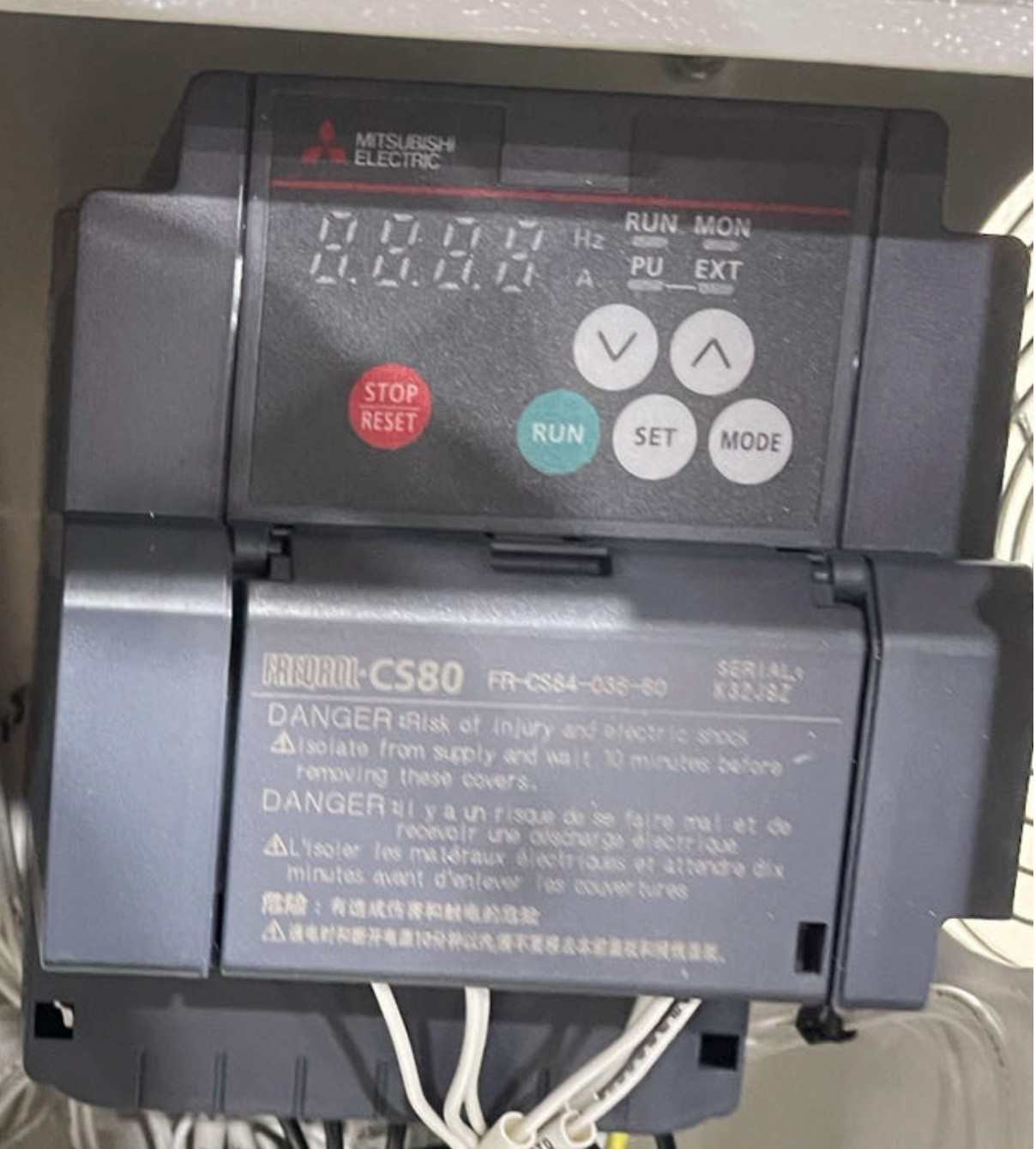
b. The configuration of frequency control
With the use of this feature, the decoiler may flexibly alter its speed in response to demand, which improves stability and smoothes the material strip discharge while lowering jitter.(When the client uses the decoiler with the leveling machine, for instance, the material won't be stretched and bent by the abrupt startup because of the frequency converter speed regulation, which makes the device relatively stable at startup.Additionally, it is comparatively stable when stopped, and the coil's inertia prevents the material from coming loose.)
c. Decoiler Device for pressing an arm cylinder
To prevent bulk material when the coil is uncoiled, the cylinder pressing arm presses the material's outside ring. Customers can typically be recommended a material when its thickness is greater than 2 mm.
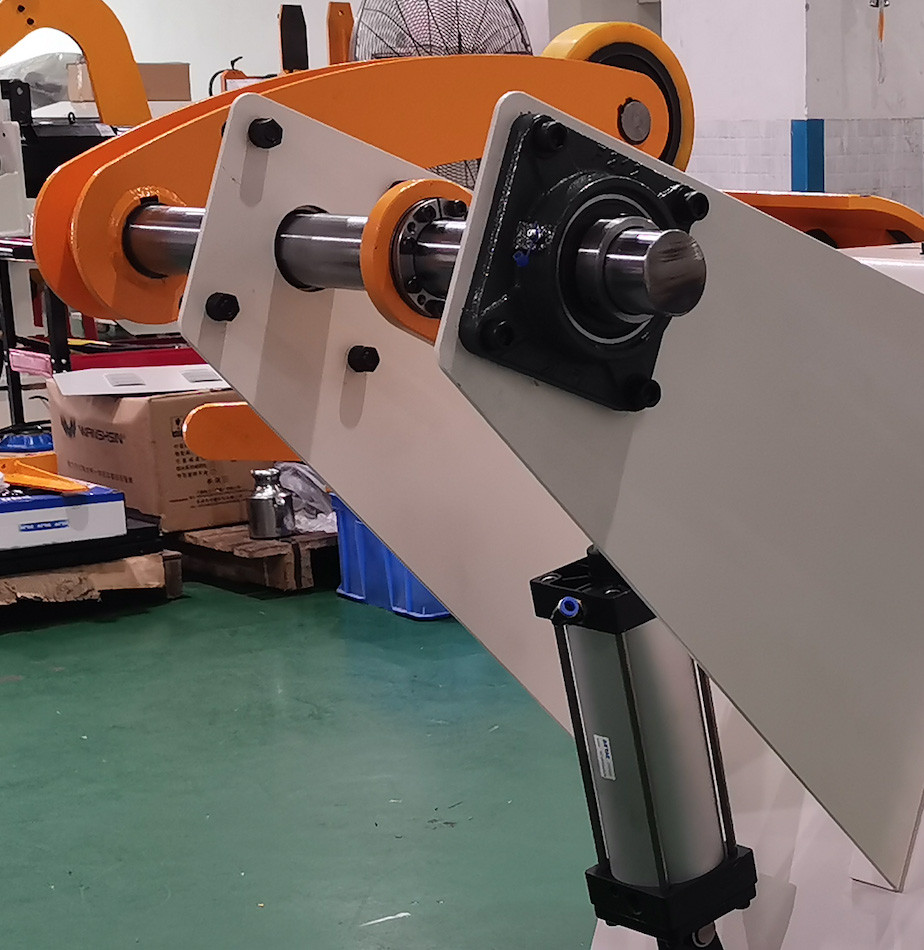
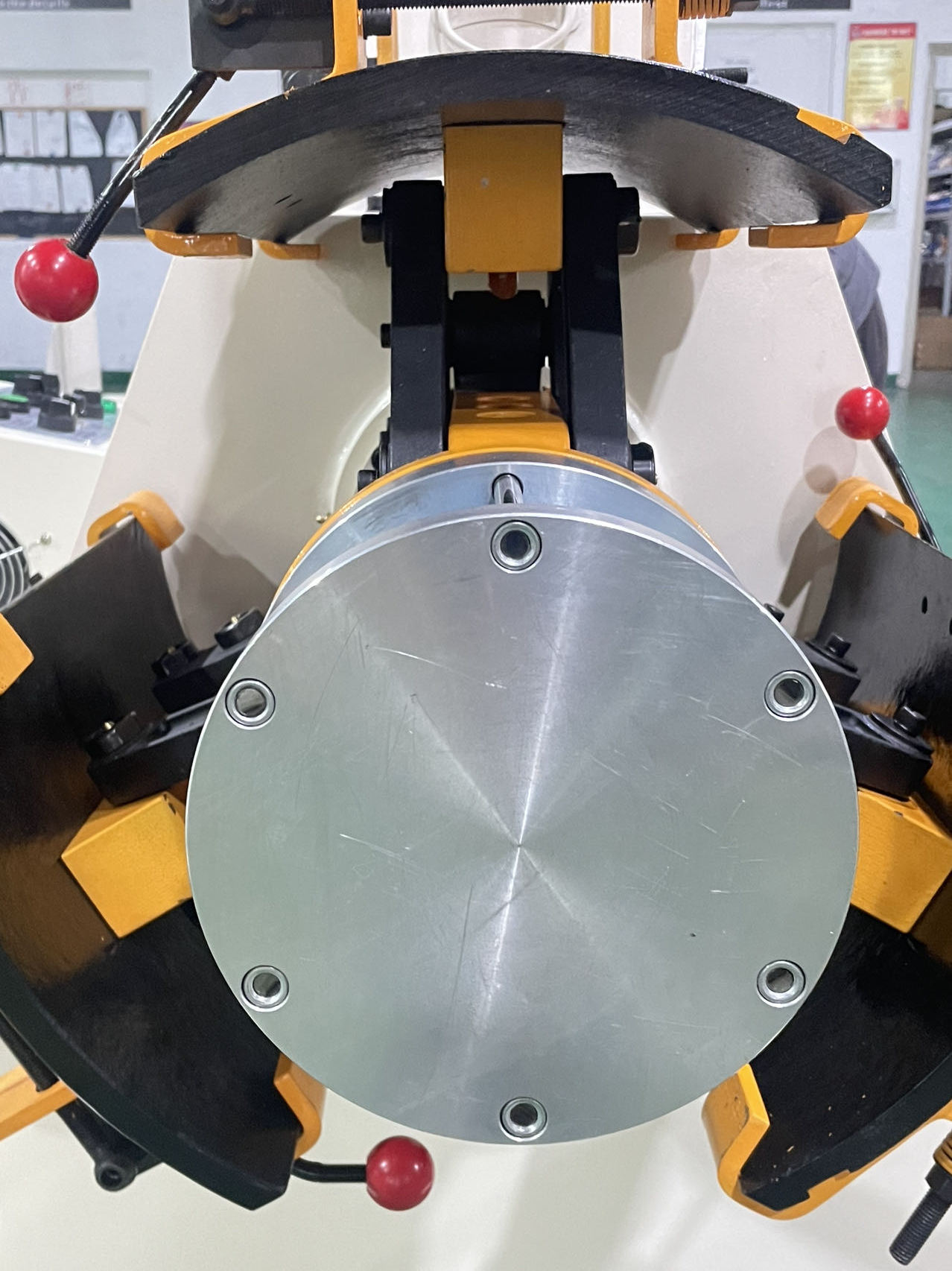
d. Modification of the outer and inner diameters
The international coil has an outer diameter of 1200 mm and an inner diameter of 508 mm.
The maximum outer diameter is 1200mm, and the inner diameter range is 450-530mm. It must be modified if it is outside of this range.
e. A Decoiler device for hydraulic
By installing this mechanism on the decoiler in place of the conventional manual expansion device, the labor intensity of manual expansion is decreased while also guaranteeing that the decoiler can be fully stretched. Customers are typically able to receive recommendations for coils weighing three tons or more. (Obviously, in order to save labor, some clients also use it when it weighs less than three tons.)
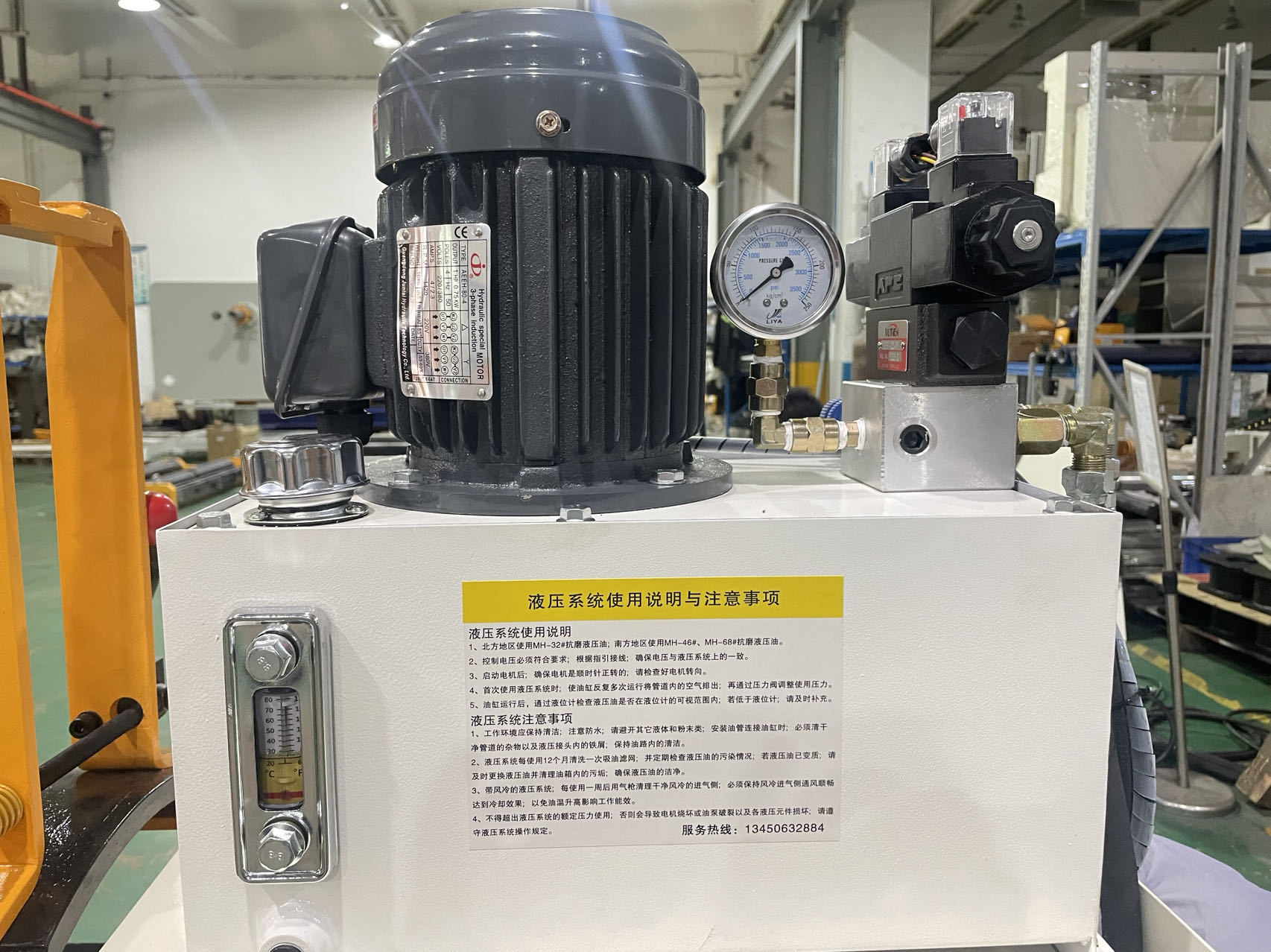
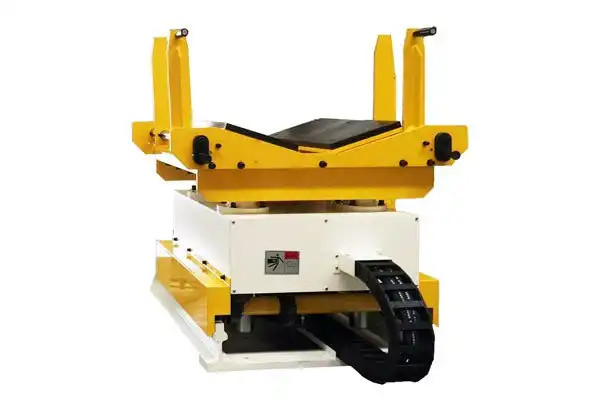
f. Decoiler Trolley with hydraulic loading (coil car)
Customers are advised to utilize it when the coil weighs more than three tons or the material is extremely wide.
g. An induction device that uses photoelectric or proximity switches
used in place of conventional touch sensor rods to unwind materials that are film-coated or non-conductive. (If this material is the customer, then this configuration must be used.)
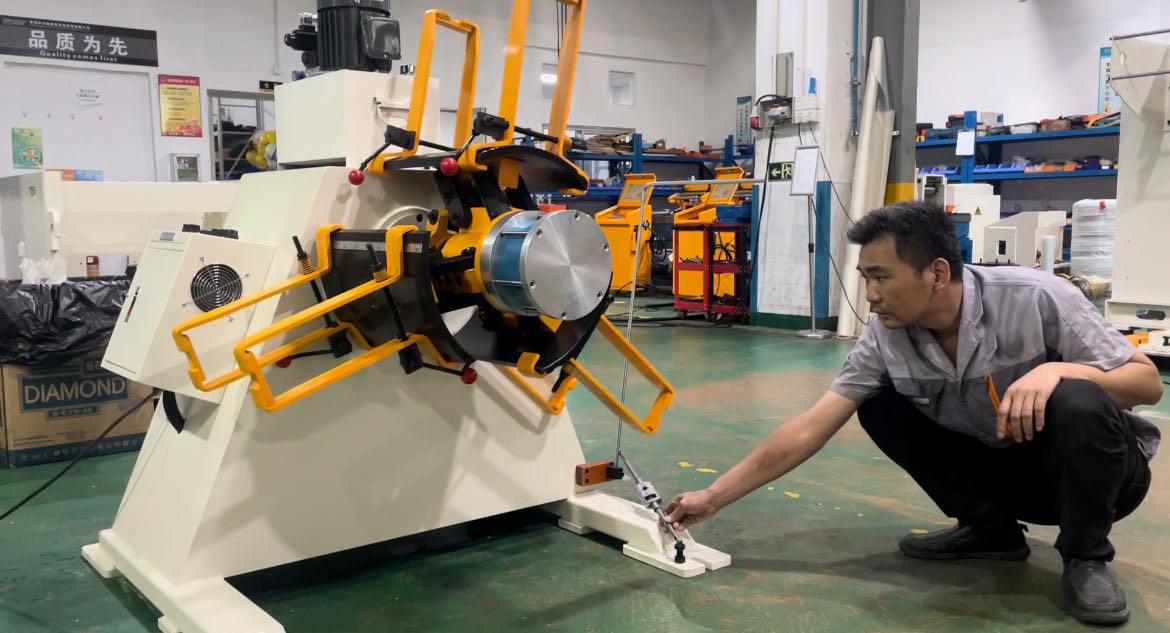
Naturally, there are other devices that can be chosen to improve the uncoiler's performance. In order for you to comprehend the mystery of the uncoiler, I will also introduce each of them individually here.
2.1. A spindle head support must be added if the coil weight exceeds 10 tons. This support can be manually adjusted, or you can opt to use a lifting reducer. If the weight exceeds 15 tons, a hydraulic adjustment is required.
2.2. A pneumatic disc braking system must be provided when the weight of the material reaches three tons.
3. Clearly state the dimensions of your own production workplace, the model, and the processing technology that will eventually be paired with the decoiler.
Further requirements for the decoiler will arise from the need to determine whether it needs to be paired with other models and processing technologies in the future.If the surface of copper and aluminum needs to be coated, then this is the time to add a second coating device, regardless of any restrictions on the material's surface. In order to keep the material from being dragged, variable frequency speed regulation must be used if it is found that the material needs to be covered.
Customers find it challenging to take them all into account because there are a variety of manufacturing scenarios and needs. As a result, choosing the right decoiler is crucial, and it must be done so based on requirements in order to guarantee that it satisfies the demands of post-processing technology.
Therefore, before making a decision to purchase a decoiler, consider your essential needs. Then, speak with FANTY, and we'll offer you the finest purchasing guidance.
Issues and fixes with the decoiler
1. A decoiler mechanical malfunction.
1.1. The decoiler's actual coil material is outside of its useful life; however, it can be changed with coil material that is compatible with the decoiler that was purchased.
1.2 The decoiler's main shaft bearing is damaged, making it impossible for the equipment to function. This issue can be resolved by replacing the main shaft bearing.
1.3 The decoiler's transmission belt inside the fuselage is very loose, causing it to slip and not be able to supply power as it should. Just tightening the drive belt will fix the issue.
2. The decoiler's electric control box is broken.
2.1. A faulty connection between the external power source and the decoiler prevents it from turning on. To fix the issue, simply inspect and fix the power line.
2. 2. The time relay, intermediate relay, and AC contactor are damaged, making it impossible for the decoiler to operate normally. The problem can be resolved by simply having it fixed or replaced.
2.3. There is inadequate contact or a falloff in the decoiler's induction device circuit. The issue can be fixed with focused inspections followed by repairs.
3. The decoiler's reducer and motor failed.
If there is no sound from the motor, either there is a defective contact in the circuit or the motor has burned out. If the motor runs but produces no sound, it is important to inspect the shaft card for damage. The reducer is broken if the shaft card is damaged. The reducer typically has a low failure rate, and prior to examination, it is usually required to rule out other potential causes of failure.
How the decoiler should be maintained?
1. Make sure the decoiler is properly grounded before turning it on to prevent injury to workers or electrical appliances from faulty grounding.
2. Inspect the support tile of the decoiler's expansion and contraction reel for surface wear before using the decoiler. Simultaneously, examine the state of fastening on the pertinent bolts and sliding shafts of the expansion and contraction reel. Inspect for damage to the bearing seat and replace or fasten it.
3. To prevent electrical damage or unexpected failure while in operation, open the electric control box, inspect how the contacts are fastened, and make sure the contact parts are secure.
4. Every month, or when the decoiler's operating time reaches 260 hours, butter must be added to the main shaft bearing. It is required to open the decoiler's rear casing and change the reducer's oil every six months (or when the working time reaches 1500 hours). Note: You should change the oil up to halfway between the rod and the axle.
Decoiler FAQ
Curious about our decoilers? Our FAQs section addresses common queries to provide you with comprehensive insights into our product group. Explore the benefits, functionalities, and technical details that set our decoilers apart. Here, I will go over each of the common issues with the decoiler one at a time, covering topics like upkeep, failure analysis, and additional uses for the device.
Please click the relevant link if there is a topic about uncoilers that piques your interest.
For any questions, you can get in touch with us directly at fanty@sz-fanty.com, and we'll help you figure out the problem.
For additional details regarding the decoiler machine, see this link.
Follow FANTY Channel:
Facebook: https://www.facebook.com/Fanty1229/
Cases Study
Explore how our Decoiler Product Group has been instrumental in enhancing production processes across industries. Discover real-world applications and success stories that showcase the versatility and efficiency of our deoiler equipments.
5 products found
Always workin with automatically feeding equipment to produce all kinds of metal stamping parts.
Working with S-type straightening machine, gear feeder and high speed punch press machine for high speed stamping line.
The Heavy Duty Decoiler suitable for 2 tons above material weight and as per customer special coil material requirement.
The Hydraulic decoiler keeps smooth & controlled unwinding of coils, minimizing any potential disruptions during the production process.
2000kgs Coil Loading Flat Decoiler Designed For High Speed Punching Machine
Categories
subscription
Please send your message to us
Contact FANTY today for efficient solutions that optimize your manufacturing processes. Our expertly designed equipment ensures safe and precision steel coil handling, enhancing your production efficiency. Get in touch with us now to elevate your manufacturing capabilities.
- Tel
- *Title
- *Content